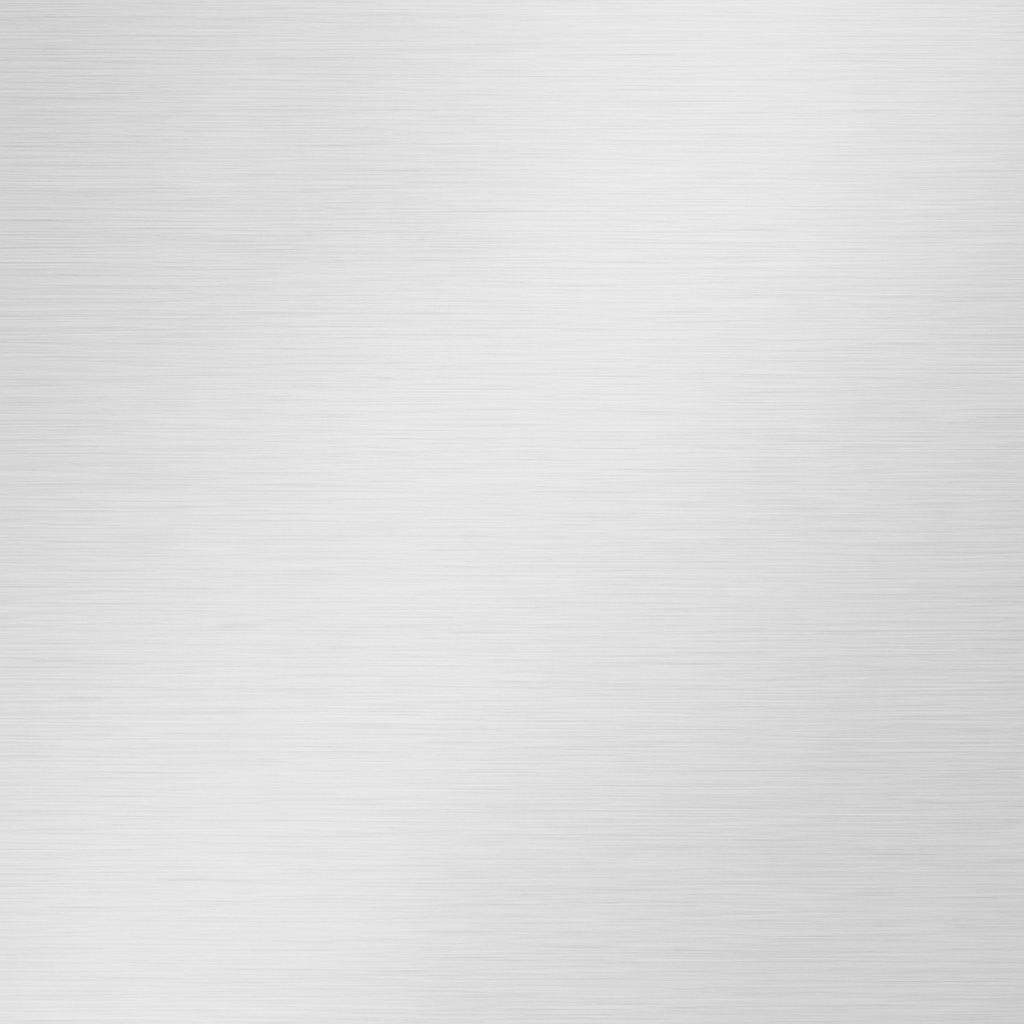
Ihr Produktionserfolg beginnt jetzt
Ohne Maschinenwechsel, ohne unnötige Kosten, in 3 Monaten kann Ihre Produktion die Erwartungen übertreffen.
GetRealOpti – Experte für Prozessoptimierung und industrielle Implementierungen.
Wir sind kein klassisches Beratungsunternehmen.
Wir optimieren Prozesse, schulen Teams und stabilisieren Maschinen – direkt in der Produktion, ohne Umwege.
Das ist Optimierung der neuen Generation.
Keine Theorie, sondern Transformation mit Wirkung.
Wir verkaufen keine Präsentationen – wir liefern Checklisten.
Keine Versprechen – sondern Resultate.
GetRealOpti bedeutet: Effizienz, Qualität, Sicherheit. In der Werkshalle – nicht im Besprechungsraum.
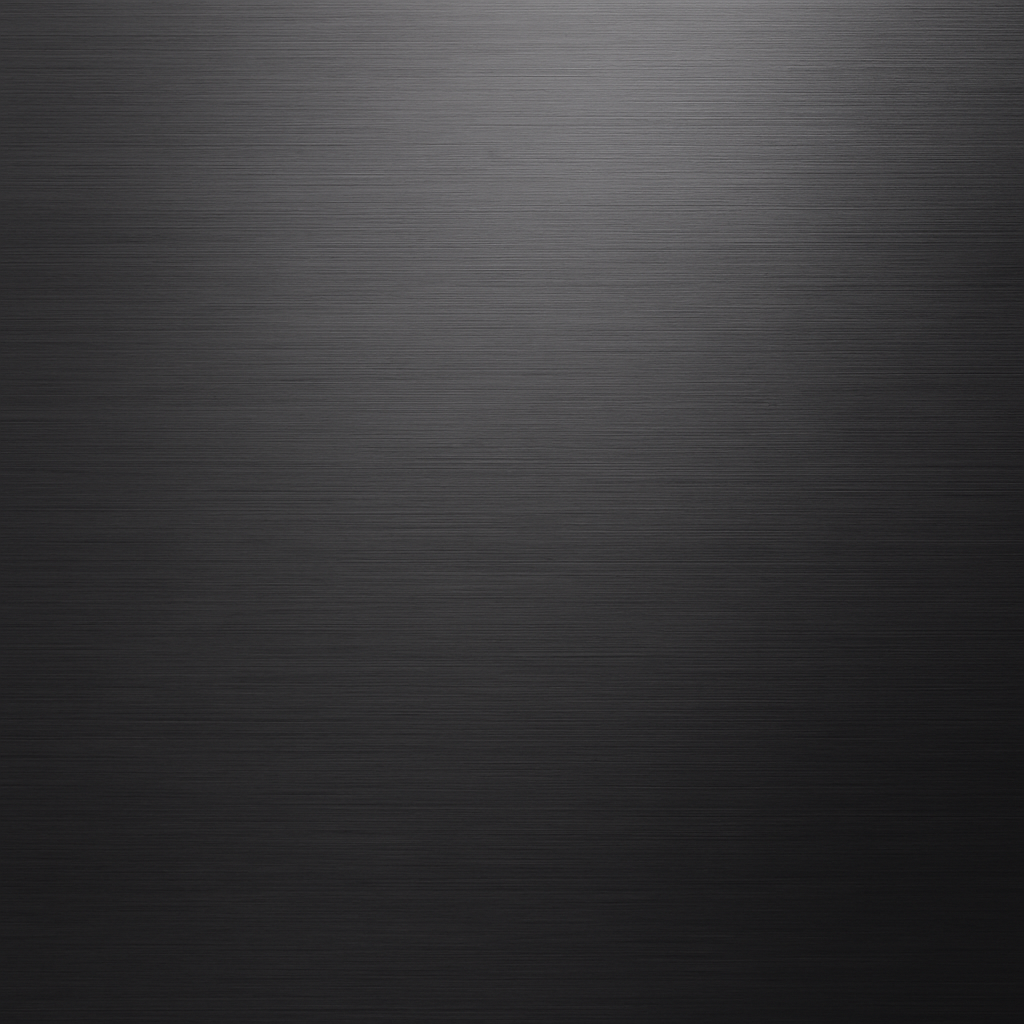

Warum sollten Sie uns wählen?
Tiefgehendes Prozessverständnis
Durch unsere Erfahrung direkt in der Produktion verstehen wir Prozesse nicht theoretisch – sondern operativ, systemisch und praxisnah.
Fokus auf messbare Ergebnisse
Unsere Maßnahmen sind zielgerichtet: kein Overhead, keine PowerPoint-Konzepte – sondern konkrete Verbesserungen in Effizienz, Kosten und Durchsatz.
Schnelle Umsetzung, keine Umwege
Wir testen und optimieren direkt vor Ort. Unsere Lösungen greifen dort, wo andere noch analysieren.
Internationale Standards – integriert, nicht nur erfüllt
TPM, Lean Six Sigma, ISO – zertifiziert & vollständig in Ihre Produktion eingebettet.
Individuelle Lösungen statt Standardansätze
Jedes Unternehmen ist anders – unsere Lösungen auch. Wir passen unsere Umsetzung exakt an Ihre Struktur, Branche und Ziele an.
Mehr über unsere Methodik und Beispiele aus der Praxis
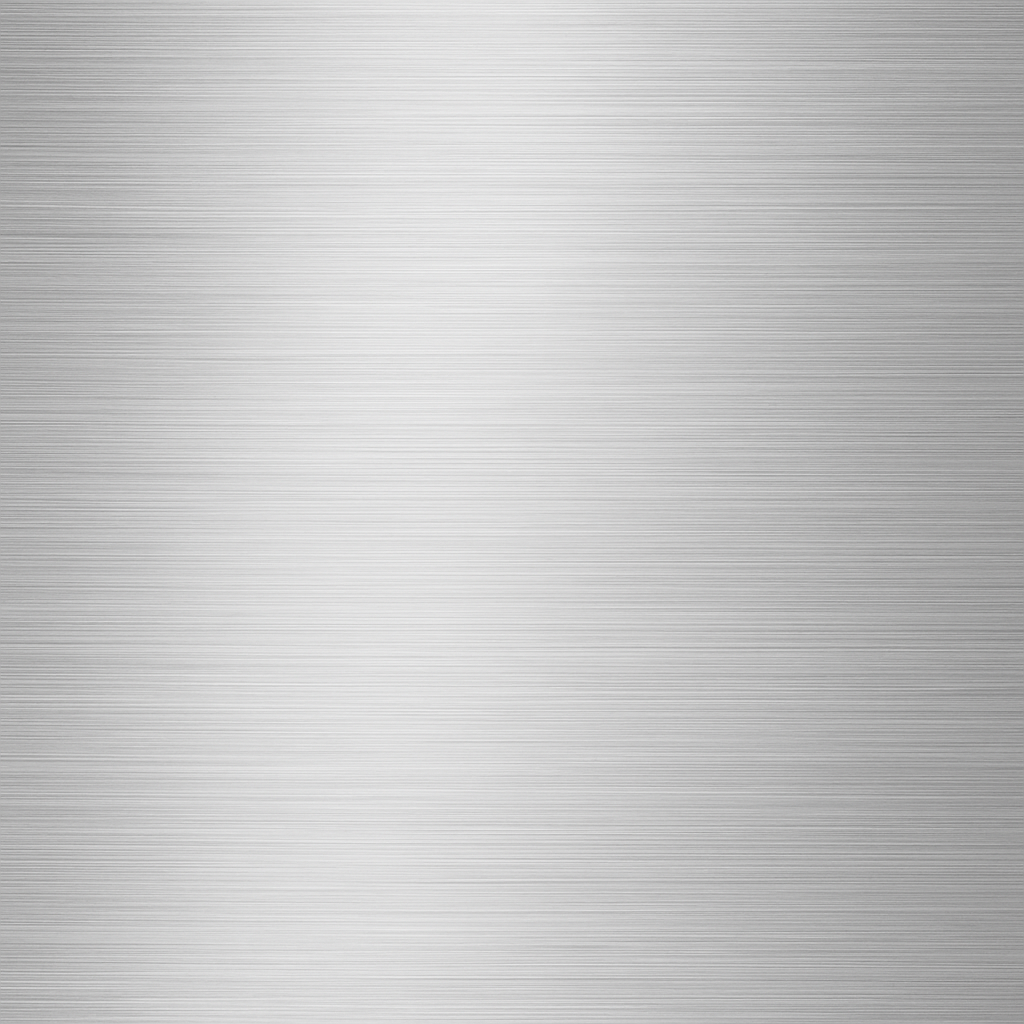
Unterstützung bei Maschinenimplementierung und Relokationen
Eine gut eingeführte Maschine ist die Grundlage jeder erfolgreichen Prozessoptimierung.
Doch genau hier fehlt oft das entscheidende Bindeglied zwischen Technik und stabiler Produktion.
GetRealOpti ist dieses fehlende Glied.
Wir unterstützen Maschinenhersteller und Relokationsfirmen dort, wo das technische Projekt endet – und die operativen Herausforderungen beim Kunden beginnen.
Dank unserer Begleitung erhält der Endkunde:
eine stabil laufende Maschine,
ein geschultes Team,
und einen einsatzbereiten Prozess – ab dem ersten Tag.
Sie liefern die Technik oder das Projekt – wir sorgen dafür, dass es funktioniert.
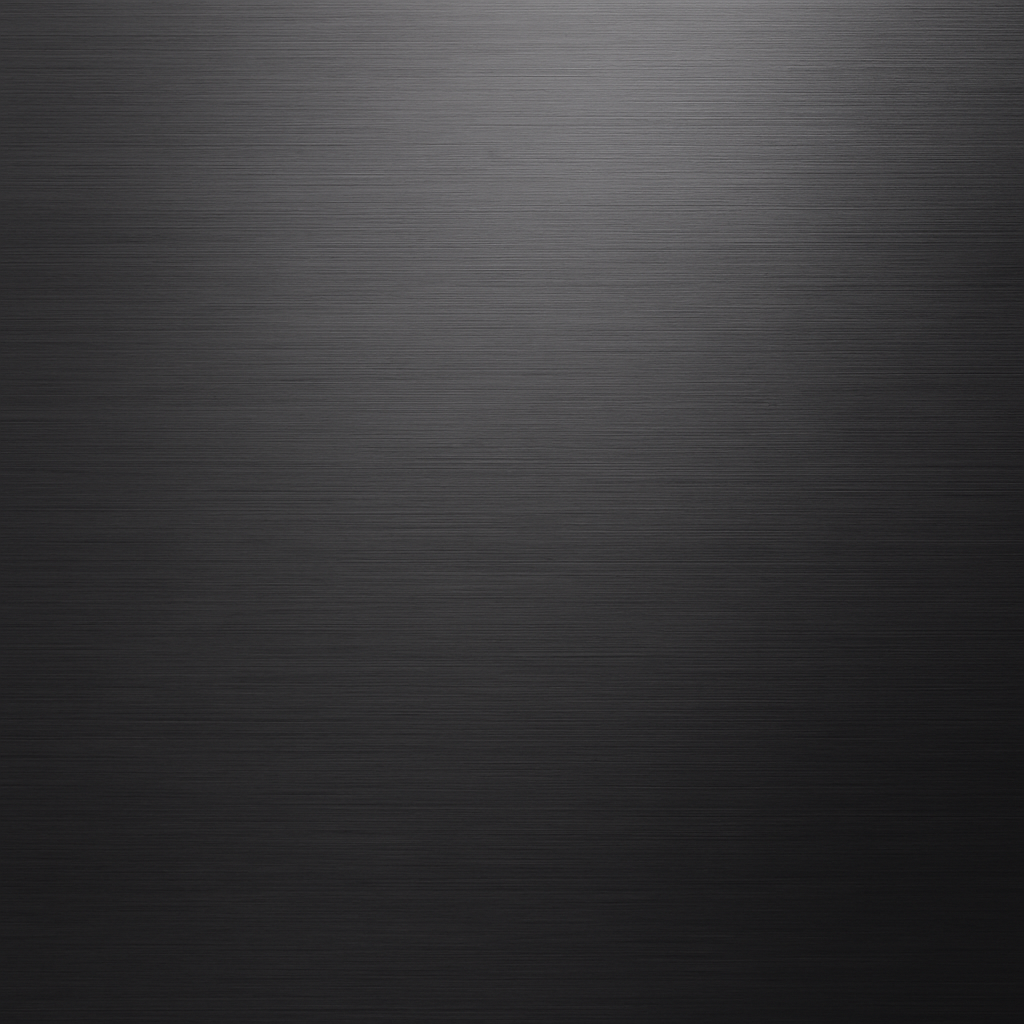
Fallstudien
-
- Produktionssteigerung um 300% nach 3 Monaten durch Einführung eines Akordsystems und Umstrukturierung der Arbeitsabläufe.
- Reduzierung der Fehlerquote um 30-50% dank verbesserter Qualitätskontrollen und schneller Fehlererkennung.
- Schnellere Produktion nach nur 1 Monat, mit erheblichem Anstieg der Produktionsmenge.
- Minimale Investitionen: Optimierungen der vorhandenen Ressourcen und Arbeitsprozesse ohne große Kapitalausgaben.
-
- Produktionsleistung um 85% steigern – von 20.000 auf 37.000 lackierte Teile pro Schicht
- Farbwechselzeit um 35% reduzieren
- Schleifkapazität um 140% erhöhen
- Ausschuss um 30-50% senken dank schneller Fehlererkennung
- Minimale Implementierungskosten (hauptsächlich Reparaturen bestehender Maschinen)
-
Porsche- und BMW M-Power-Motoren sind Hochleistungsaggregate, die eine präzise Diagnose und spezialisierte Modifikationen erfordern. Im Rahmen unserer Arbeit haben wir zentrale Probleme wie übermäßigen Ölverbrauch, Überhitzung der Zylinder sowie Schäden an der Kurbelwelle und am Vanos-System behoben. Durch den Einsatz verstärkter Zylinderlaufbuchsen, Härtung der Kurbelwelle und die Optimierung des Schmiersystems konnten wir die Haltbarkeit der Motoren erheblich verbessern, den Ölverbrauch um 90 % reduzieren und die Gesamtleistung optimieren.
Zeit ist Geld - kontaktier uns jetzt und lass uns anfangen!

Stimmen aus der Praxis.